If you are contemplating abandoning your land dwelling and taking up a life on the water, you have a lot of options to consider. Do you buy used or new? Where do you want to live? How will you be using the boat? How much space do you need? The vessel designs and choices are endless—trawlers, tugboats, houseboats, sailboats, and barges, to name a few. Everyone’s situation is different, but here is a story of what my wife and I chose, and what the process was like, in case it helps you in your decision process.
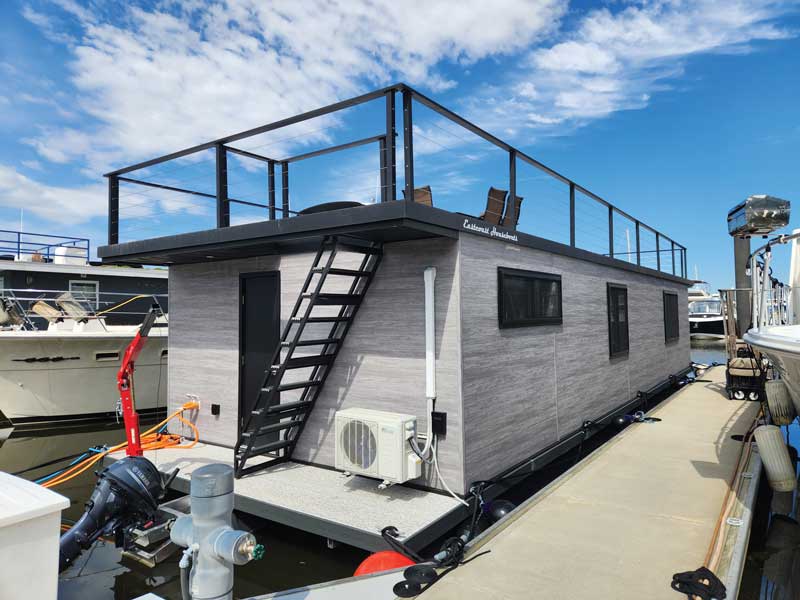
Considerations
My wife and I have been living at the Wharf Marina in Washington, DC, for several years. We lived on a wonderful barge while contemplating what we wanted in a new home. During the first two years we pored over options, recognizing early on that we really liked the amenities, spaciousness, insulation, and comfort that barges, and some houseboats, provide. Since we had been sailing for years and had plenty of dinghy and cruiser options for exploring the Chesapeake Bay watershed, we opted for a fully customizable 50-foot houseboat.
Features & Amenities
The time we spent beforehand as full-time liveaboards was time well spent. We learned a lot from friends, neighbors, and boarding countless vessels. As a result, our thoughts evolved as to what features and amenities we wanted in a custom-built vessel. Some features that would have been important two years prior turned out not to be, and other features that would not have occurred to us beforehand had become priorities instead.
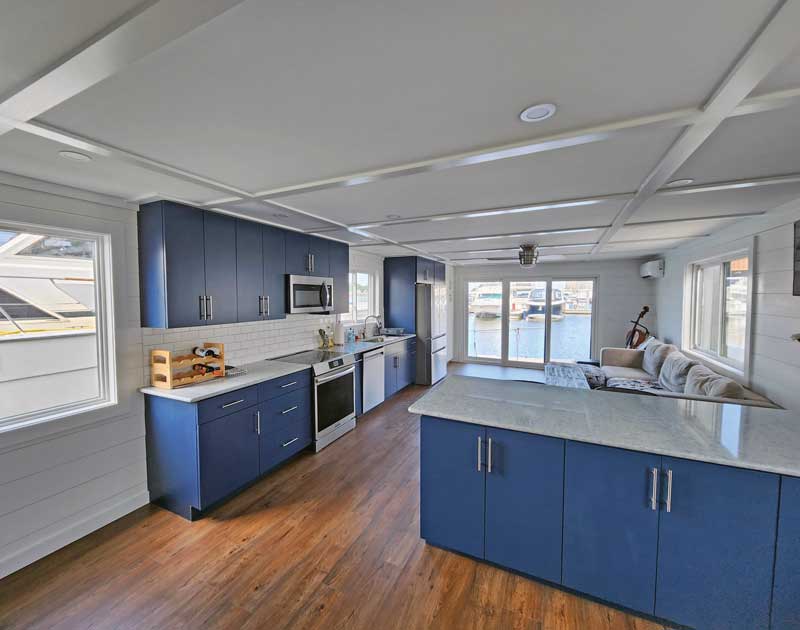
We had arrived at a short-list of must-haves versus nice-to-haves by the time the design process began. High on the list of must-have priorities was incorporating energy-efficient and water-efficient traditional home appliances. We went with a 36-inch LG refrigerator, Frigidaire induction range, Electrolux washer and dryer, and KitchenAid dishwasher. In addition, we were particularly interested in a well-insulated vessel, coupled with a highly effective A/C and heating system. The virtually silent Senville mini-split units installed in the living room and bedroom, combined with energy efficient windows and thick insulation, provided a highly effective combination this summer, and a surprisingly low electric bill.
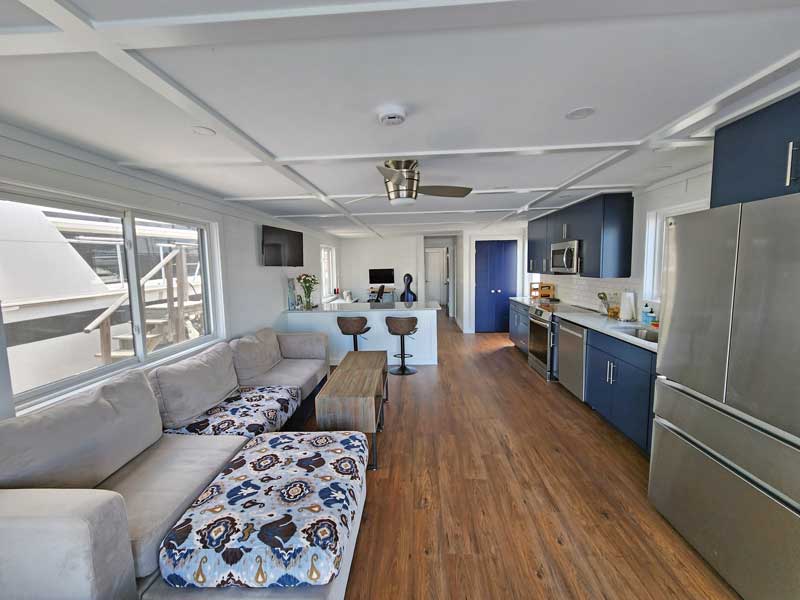
Some of the nice-to-have ideas proved overly complicated or too expensive for the benefit they would yield. These ideas included a heated upper deck, a system for treating and recycling greywater, and a retractable pergola/bimini. Other nice-to-have features turned out to be less interesting once the vessel started to take shape, such as an electric fireplace and a divider/partition between the living room and office/guest room. We instead went with a much more open plan, with fully modular and quickly rearrangeable furniture. A nice-to-have idea that actually worked out brilliantly was the builder’s incorporation of a receiver on the engine mount, which enabled us to attach a bracket for an outboard engine hoist.
Logistics
Building a new vessel can be a big-time commitment. Expect to work with the builder to arrange a lot of logistics (choosing the staging/assembly marina, towing, a multitude of contractors, etc.), in order to get your vessel on time. Also, I recommend keeping your own detailed and meticulous checklist of questions, to-dos, and reminders, between yourself and the builder, since important details can otherwise get lost and hold up subsequent stages of the build process.
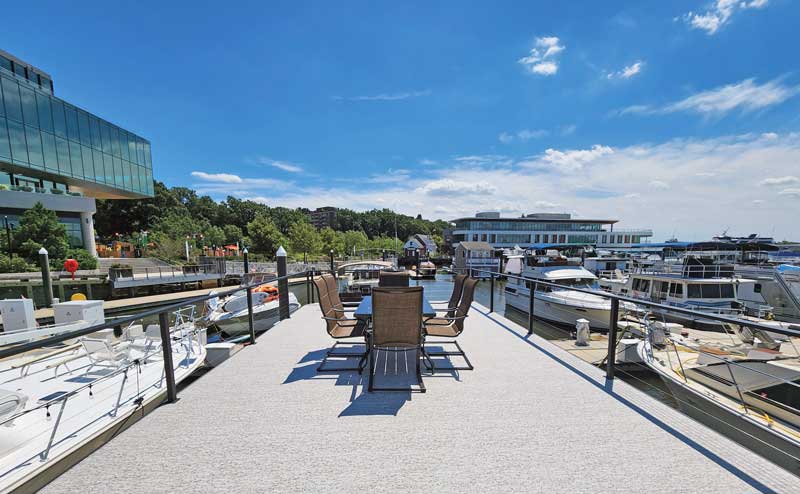
Keep in mind that this is the equivalent of remodeling every room in a house, all at once. Numerous steps have to happen in a certain sequence, some things cannot wait, and lots of items require significant lead-time for delivery. Also, expect to make frequent trips to the manufacturer, if you want to ensure that the vessel meets your expectations (which is the main reason for doing a custom-build, in my view). Photos will not necessarily give you the spatial understanding you might want.
Design
In coming up with our design preferences, we had to think about how we had been living, versus how we wanted to live, versus reality. For example, what if one spouse hangs their clothes and the other folds their clothes, but the reality of the new space is that there is not enough room for both shelves and rods? In most cases we were able to find a design solution that worked for both of us, but we had to keep thinking several steps ahead, before some steps were etched in stone.
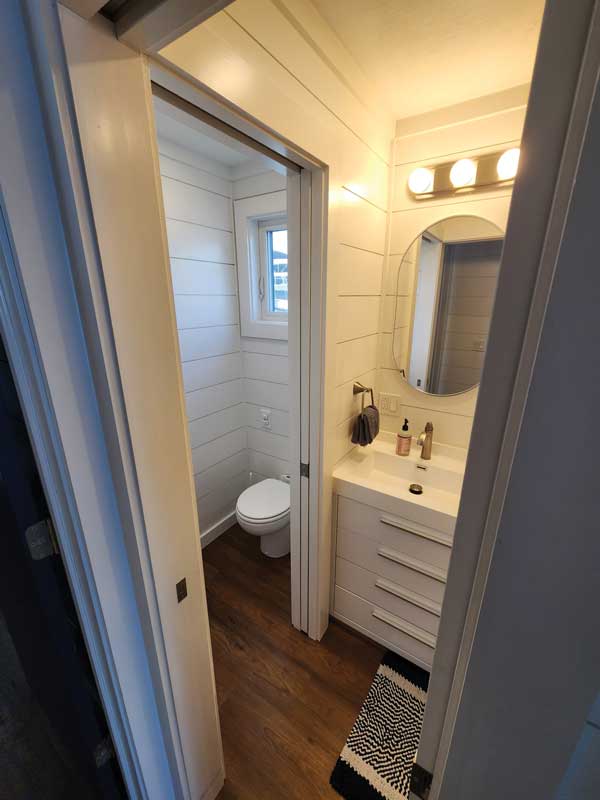
We also had some interesting conversations with the builder about vessel balance. Just determining the weight and location of the appliances in an empty vessel is not sufficient. You will also have to factor in the weight and location of your furniture, and how the filling, emptying, and movement between freshwater, greywater, and blackwater tanks will affect the vessel’s balance over the course of the week.
Thinking Ahead
During my frequent visits to the manufacturer, I also endeavored to document the build process. I did so in order to ensure that I understood each stage of how the vessel was constructed, what was actually behind the walls, and what was underneath the flooring. The other reason for doing so was to create my own custom-built owner’s manual (both in digital and physical form). This manual contains step-by-step photos of key systems on the vessel, a library of all onboard system manuals (appliances, water heater, etc.), tutorials for vessel components and systems not covered in these manuals, a detailed parts inventory for every vessel component I could identify, and maintenance/inspection schedules for all key vessel components.
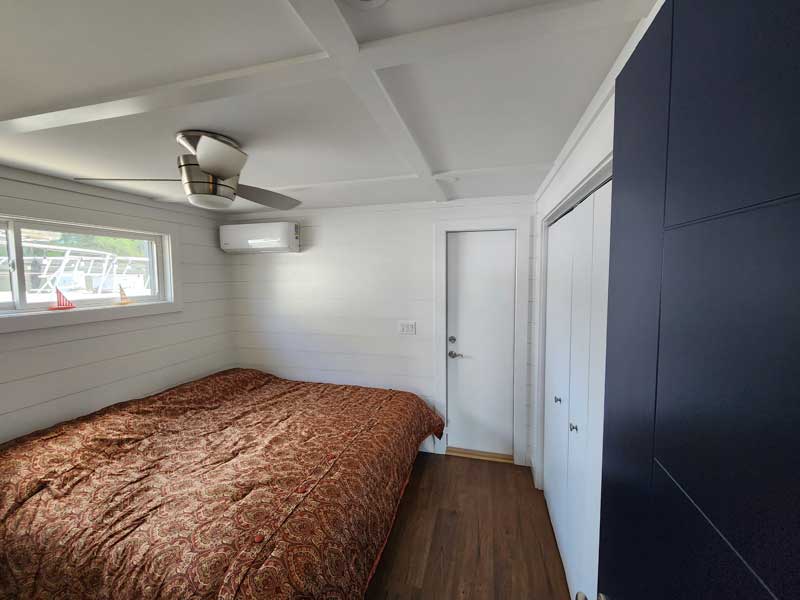
For years I have created my own user manuals for the vessels I used or owned, but developing one throughout the construction process has enabled me to capture features and attuned me to details I might not have thought about if I had purchased a used vessel or a fully constructed new vessel. The user manual has also helped me to internalize important issues, and to customize instructions for the unique characteristics of this particular vessel that would not otherwise be captured in an off-the-shelf manual.
Timing
Having worked on a lot of infrastructure projects over the years, one thing I know is that construction projects rarely keep to schedule. Fortunately, ours arrived by our deadline. The entire process from the first conversation to the vessel’s arrival was 16 months. After a few months of conversations, brainstorming, contract discussions, and back-and-forths on design, the actual build process took about seven months. Had I not had great neighbors to consult, it likely would have taken us a lot longer to do our homework and figure out what we wanted.
Hopefully this experience will be of help as you weigh your options. If readers have questions, they can reach out to me at [email protected].
By Nathan Younge