Exposure to moisture is an undeniable aspect of boat ownership. To a degree, boat owners must live with it; however, there are a handful of places where it’s simply not acceptable.
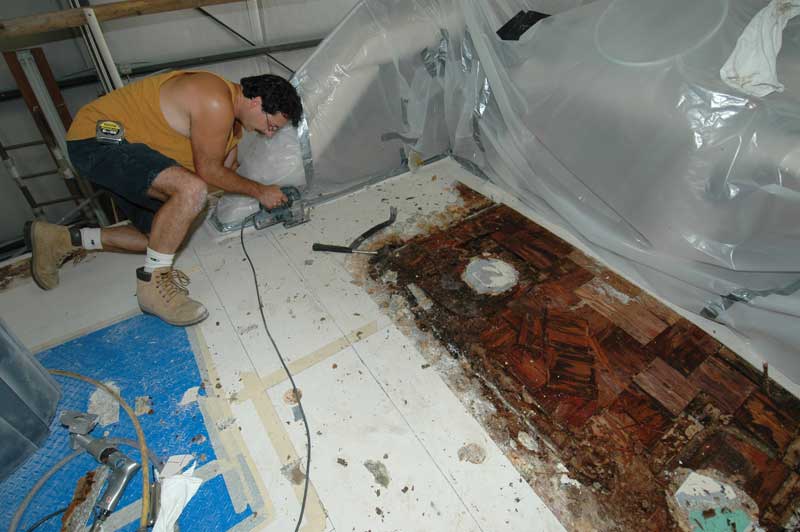
Cored Composites
Look around any boat yard, boat show, or marina, and you’ll see acres of shiny gelcoat beneath which lies glass fiber reinforced plastic (referred to as “FRP” in the industry), otherwise known as fiberglass. In most cases, primarily for cabins, decks, and hulls above the waterline, as well as on some hulls below the waterline, you’ll find a core material sandwiched between still more fiberglass “skin.” This construction technique, referred to as cored composite construction was first used in aircraft production during World War II (which included the famed British Mosquito fighter bomber and the American PBY flying boat). It revolutionized boat building, while making boat ownership more affordable and more practical. Owners no longer needed to be shipwrights to maintain their vessels. Pound for pound, cored composite construction, which emulates an I-beam, is immensely stiff and strong.
For all its indispensable value, cored composite construction suffers from one, sometimes fatal, weakness: water intrusion, and the decay and delamination to which it can lead. Depending on the core material, it may be end grain balsa wood or one of a variety of synthetic “foams” or honeycomb designs, the propensity of the core to absorb water can be prolific. Additionally, if the channels between core segments, called “kerfs,” are not filled with resin or proprietary core installation putty during the construction process, as they should be, then these voids can also fill with water and allow it to travel, in some cases feet or yards, accumulating significant excess weight.
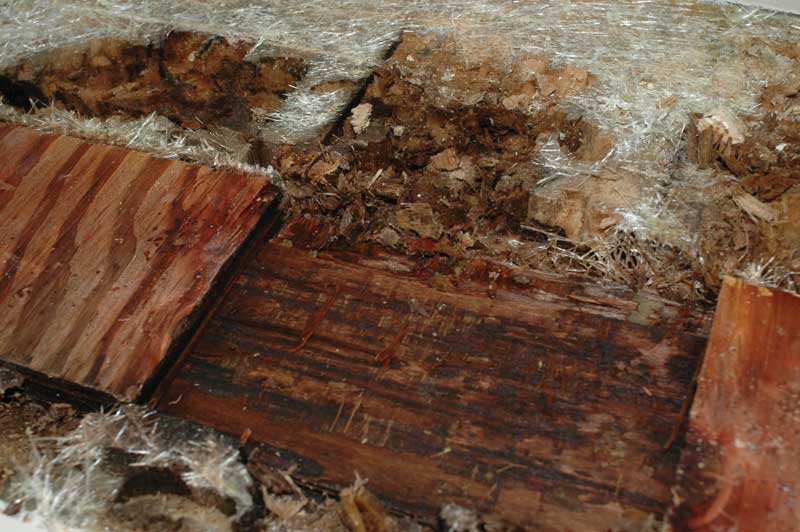
Once water enters the core, a range of maladies can occur. If it’s organic, such as end-grain balsa, of course it can decay. When that happens, adhesion is lost between the core and the inner and/or outer skins, otherwise known as delamination. Think of the “flats” of the I-beam detaching from the upright section, which results in a loss of stiffness. In extreme cases the core material can turn to a wet mulch-like mush. While closed cell synthetic foam cores don’t rot per se, they can deteriorate when continuously exposed to water. If the saturated core is exposed to freezing temperatures, the trapped water will freeze and expand, which damages the core, and leads to delamination.
Most of these water intrusion problems can be prevented by the boat builder in the design and construction process. In many cases, however, in spite of the best efforts of builders, problems begin after the vessel has been completed, when aftermarket hardware such as life rafts, antennas, transducers, canvas brackets, and even snaps are installed. Those installing these components penetrate the core material with drills, saws, and fasteners, which then rely on polyurethane sealant, the lifespan of which rarely exceeds a few years, to prevent water penetration.
This approach is a losing battle at best. The moisture meter shown on page 55, adjacent to a weather deck pad eye, confirms this unfortunate yet common scenario, which frequently and predictably occurs adjacent to deck hardware and its fastener penetrations.
Fiberglass Osmosis and Blisters
Ironically, the hot tub and spa industry faced the osmotic blister problem in the 60s, however, the marine industry had to re-learn these hard-won lessons. As it turns out, hot chlorinated water is the ideal vehicle for promotion of osmotic blistering. Their response was to get rid of gelcoat altogether, opting for an acrylic-sheet skin instead. Further study revealed that acrylic is actually more permeable than good gelcoat that’s applied in the proper thickness. The key to acrylic skin’s success for the hot tub folks was its lack of water-soluble materials, or WSMs. WSMs, as we’ll see, are the primary villain in the fiberglass blister saga.
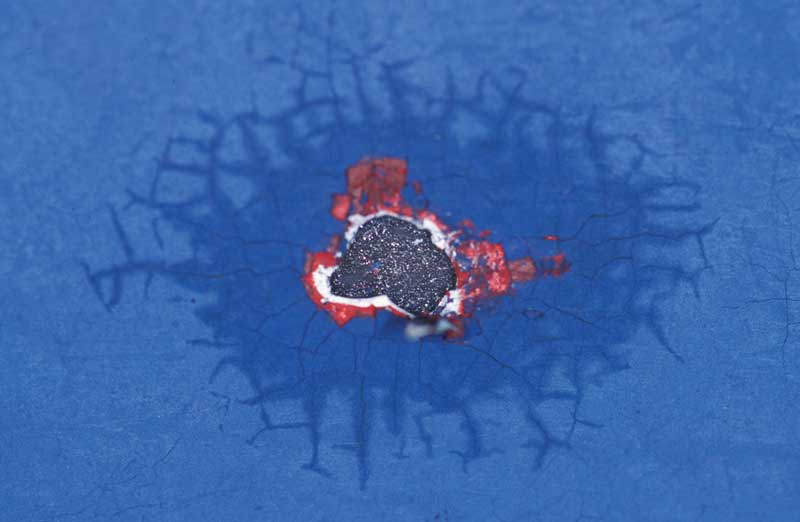
In simplified form, the chemical processes that must occur for blisters to form are as follows. Water soluble materials (binders and couplers used in fiberglass fabric, as well as thixotropes such as fumed silica, which prevent resin from being too thin and runny) must be present beneath a semi-permeable membrane—in this case the gelcoat or outer layers of fiberglass laminate. Water molecules, which are comparatively small and slippery, find their way through the molecular gaps in the gelcoat and fiberglass laminate where they encounter the WSMs. It’s love at first sight and marriage ensues, but the offspring are anything but cute.
As with any relationship, here’s where it gets a bit tricky. Some composite experts believe that many of the WSMs aren’t present in the laminate immediately after the vessel goes into service. Rather, it’s only after long-term immersion that the process of hydrolysis, also known as Le Chatelier’s principle, begins to work on the laminate, actually taking apart the resin matrix molecule by molecule. The result is that water-soluble components begin to appear in the laminate.
The next process, the actual cause for the blisters themselves, then takes over. According to Thomas J. Rockett, PhD, a research professor at the University of Rhode Island and co-author of the US Coast Guard funded study, “The Cause of Boat Hull Blisters,” water molecules enter the laminate via a process known as permeation. That in and of itself is not a problem, as long as the water doesn’t react with anything on its journey through the laminate.
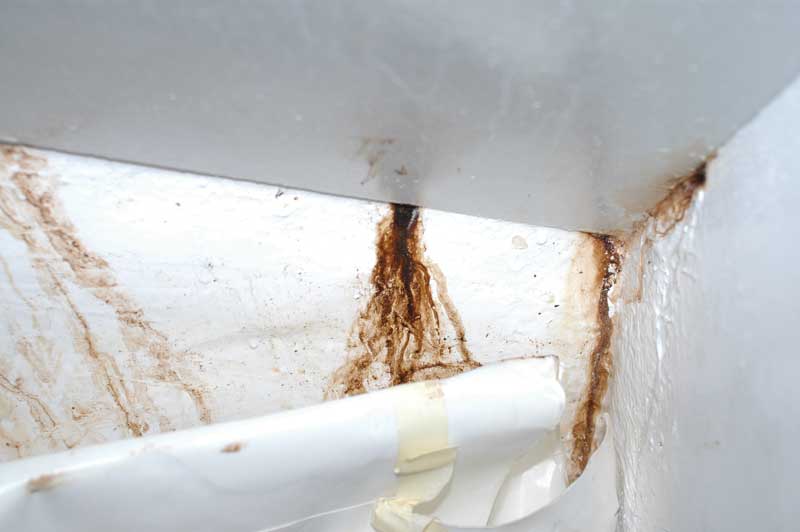
Nearly all plastics, including FRP, are to some degree permeable. The difficulty occurs when the water does encounter a reactionary agent, such as a WSM. Rockett describes the osmotic process as follows:
“Water molecules can pass through this semi-permeable membrane, the gelcoat and laminating resin layer, but the WSM molecules, because they are larger than water molecules, cannot. Since the outside water and the solution are of different concentrations, water will permeate through the gelcoat, in an attempt to dilute the droplet of solution trapped in the laminate. During the process, more water enters the droplet causing it to expand and create pressure on the surrounding hull material (this is what forms the blister that’s visible on the surface). It takes place whenever two solutions of different concentrations are surrounded by a semi-permeable membrane. When the pressure exceeds the deformation point of the hull material, it begins to flow or crack. This decreases pressure and allows more space for water to be drawn into the solution.”
From this description, it is clear to see that the blister is the final step in the hydrolysis/osmosis problem. The WSMs, coupled with permeability and the resultant susceptibility to hydrolysis of the resin matrix, appear to be the real culprits. Thus, one could conclude that the primary cause for osmotic hull blistering is the WSMs, although this borders on oversimplification because the WSMs are one of several necessary ingredients.
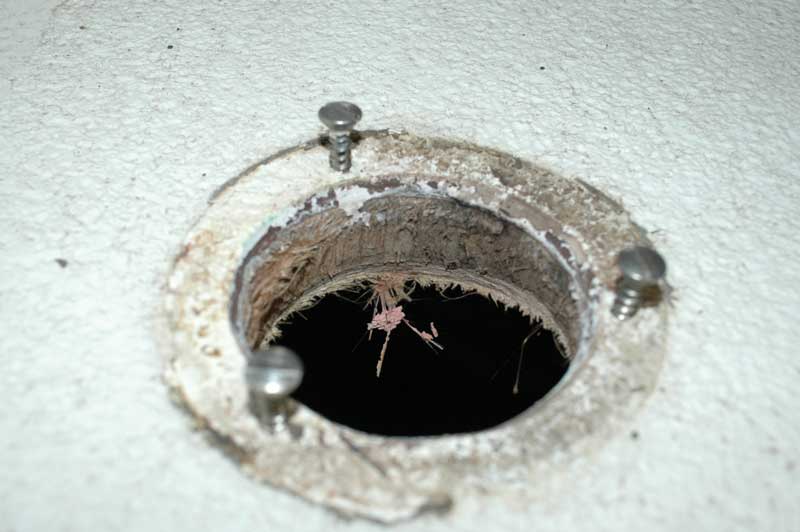
These necessary evils are the couplers that allow resin to stick to glass filaments. Binders, particularly those applied as an emulsion, which were popular in the 70s and early 80s, that are used in some chopped strand mat and combination mat/woven/knitted fiberglass cloth products, have also been identified as having strong WSM potential. Additionally, thickening agents or thixotropes are also water soluble.
In my next column I’ll discuss the best means of preventing water entry into core, and osmosis.
About the Author: Former boatyard manager, technical writer, and lecturer, Steve D'Antonio, consults for boat owners and buyers, boat builders, and others in the industry. Visit stevedmarine.com for more technical columns.